Recognizing Porosity in Welding: Checking Out Causes, Effects, and Prevention Methods
As experts in the welding market are well conscious, recognizing the reasons, results, and avoidance techniques associated to porosity is crucial for achieving durable and reputable welds. By delving right into the origin triggers of porosity, analyzing its detrimental results on weld quality, and discovering efficient avoidance methods, welders can enhance their knowledge and abilities to produce premium welds constantly.
Common Root Causes Of Porosity
Porosity in welding is primarily brought on by a mix of aspects such as contamination, incorrect shielding, and poor gas protection during the welding process. Contamination, in the kind of dust, grease, or rust on the welding surface area, creates gas pockets when heated up, causing porosity in the weld. Improper protecting takes place when the protecting gas, typically used in processes like MIG and TIG welding, is not able to fully shield the molten weld swimming pool from reacting with the surrounding air, leading to gas entrapment and subsequent porosity. Additionally, insufficient gas insurance coverage, usually because of incorrect flow rates or nozzle positioning, can leave components of the weld unguarded, permitting porosity to create. These variables jointly add to the development of gaps within the weld, damaging its honesty and potentially triggering architectural problems. Comprehending and addressing these common reasons are important actions in preventing porosity and making certain the top quality and strength of bonded joints.
Effects on Weld High Quality
The existence of porosity in a weld can considerably endanger the overall high quality and honesty of the bonded joint. Porosity within a weld creates spaces or cavities that deteriorate the framework, making it a lot more prone to fracturing, corrosion, and mechanical failure.
In addition, porosity can impede the efficiency of non-destructive testing (NDT) strategies, making it challenging to detect various other flaws or discontinuities within the weld. This can result in substantial safety and security issues, specifically in important applications where the structural honesty of the bonded parts is paramount.
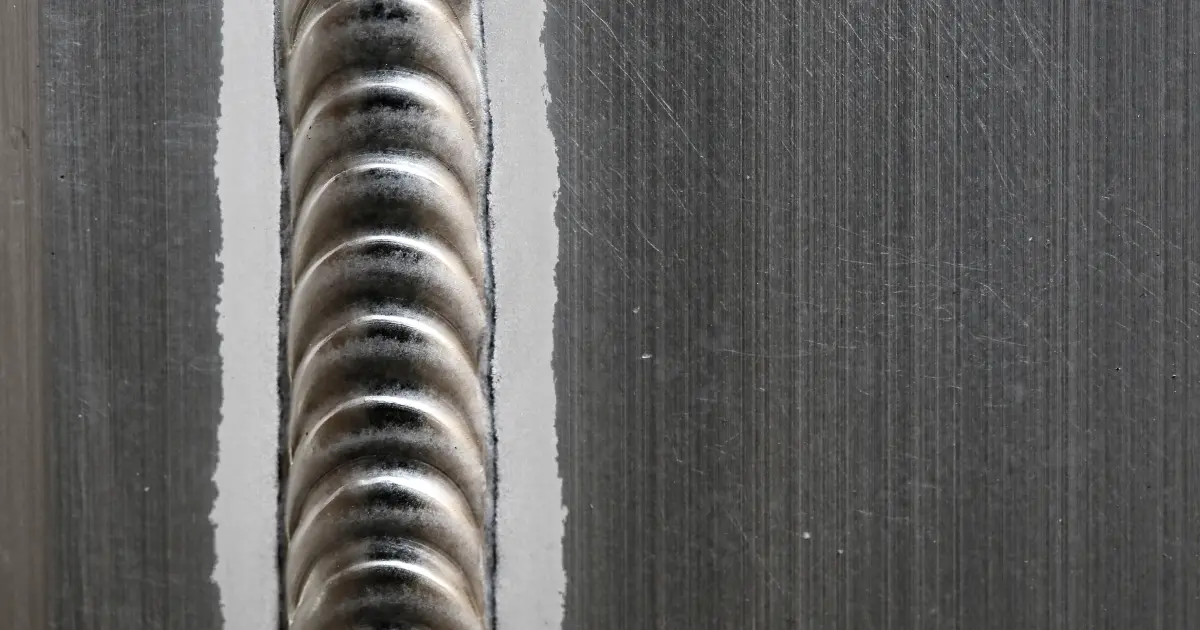
Prevention Techniques Overview
Provided the harmful influence of porosity on weld high quality, effective prevention methods are crucial to keeping the architectural integrity of bonded joints. In addition, picking the ideal welding criteria, such as voltage, current, and take a trip rate, can help minimize the risk of porosity formation. By incorporating these avoidance techniques right into welding practices, the occurrence of porosity can be substantially minimized, leading to more powerful and extra trusted bonded joints.
Significance of Proper Protecting
Correct protecting in welding plays a vital function in avoiding climatic contamination and making certain the honesty of welded joints. Protecting gases, such as argon, helium, or a blend of both, are frequently utilized to safeguard the weld swimming pool from responding with aspects airborne like oxygen and nitrogen. When these reactive aspects enter into call with the hot weld swimming pool, they can cause porosity, resulting in weak welds with decreased mechanical residential properties.

Insufficient securing can cause numerous flaws like porosity, spatter, and oxidation, jeopardizing the structural honesty of the welded joint. Sticking to correct protecting practices is vital to produce premium welds with minimal defects and make certain the durability and reliability of the bonded elements.
Surveillance and Control Techniques
How can welders effectively keep an eye on and control the welding procedure to guarantee optimum results and prevent flaws like porosity? One key approach is this article through making use of advanced surveillance innovations. These can consist of real-time monitoring systems that provide responses on specifications such as voltage, current, travel rate, and gas flow prices. By continuously monitoring these variables, welders can recognize deviations from the excellent conditions and make instant changes to avoid porosity development.

Additionally, executing appropriate training programs for welders is crucial for monitoring and controlling the welding process efficiently. What is Porosity. Informing welders on the value of preserving constant specifications, such as appropriate gas protecting and take a trip Source speed, can assist stop porosity problems. Routine assessments and accreditations can also guarantee that welders excel in tracking and managing welding processes
Additionally, using automated welding systems can enhance surveillance and control capacities. These systems can exactly control welding parameters, reducing the likelihood of human mistake and making certain regular weld high quality. By combining advanced surveillance innovations, training programs, and automated systems, welders can efficiently monitor and regulate the welding procedure to reduce porosity defects and attain premium welds.
Conclusion
